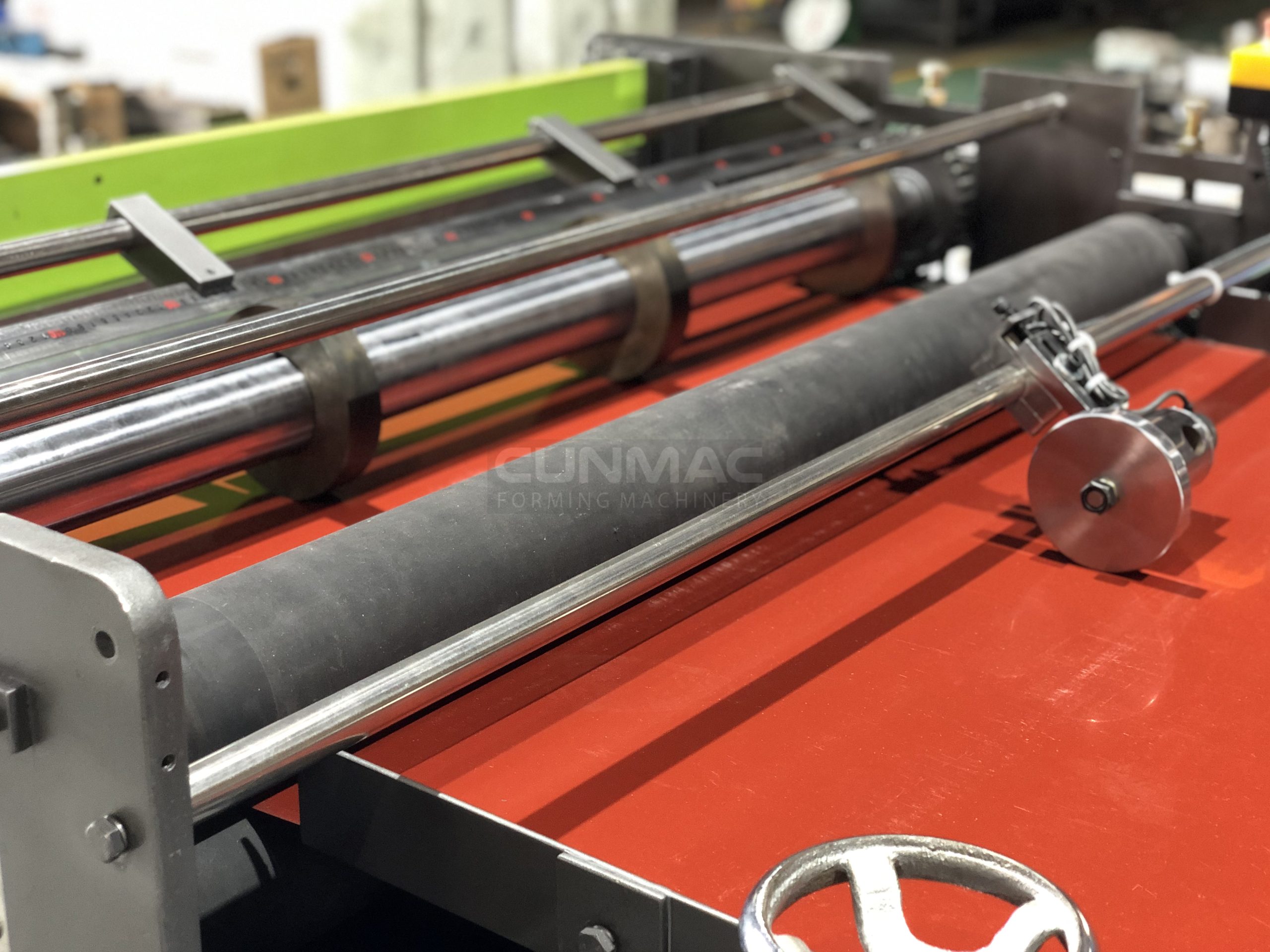
Rubber roller to guide materials in
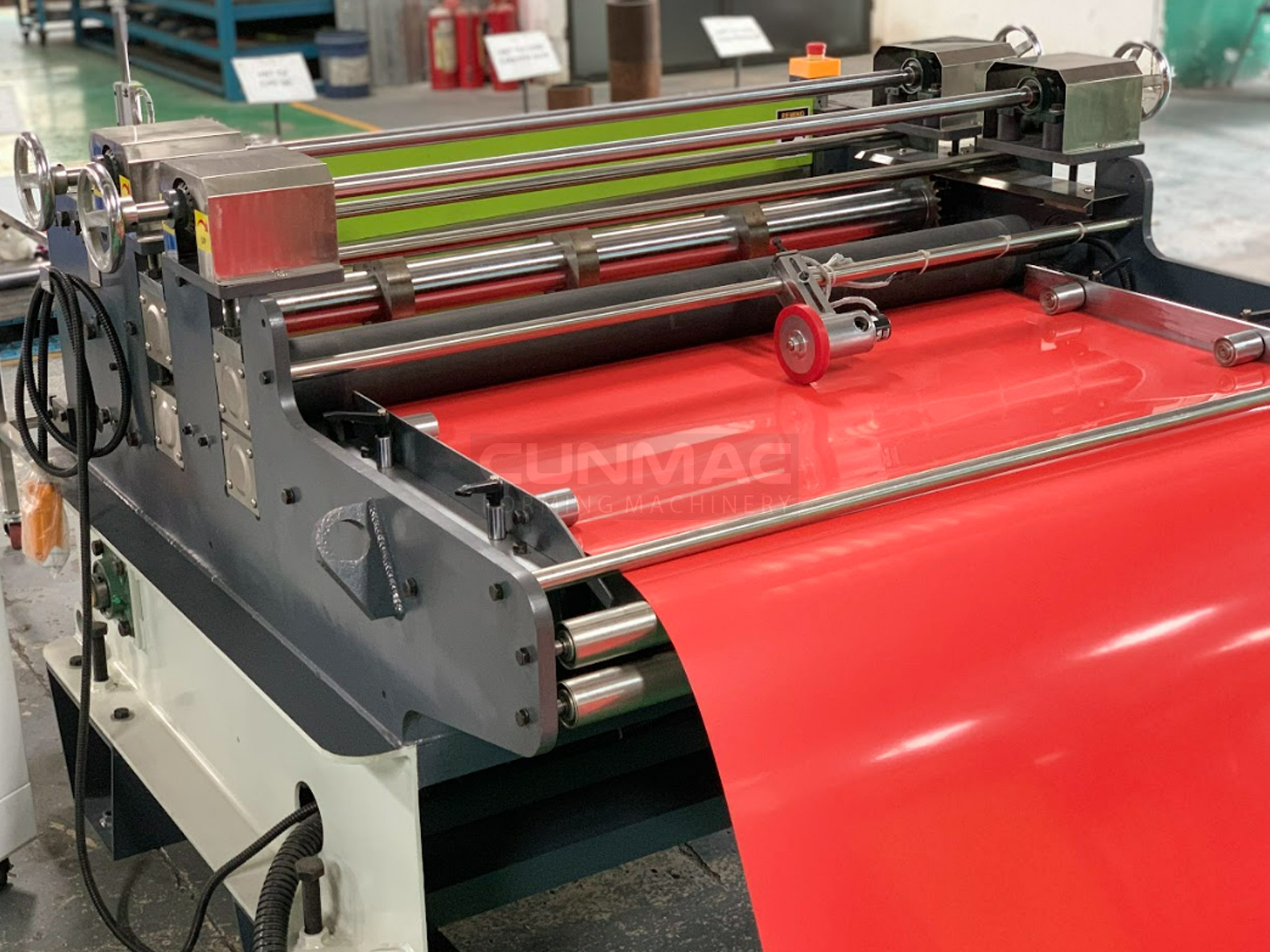
Feeding coil can change the width of coil
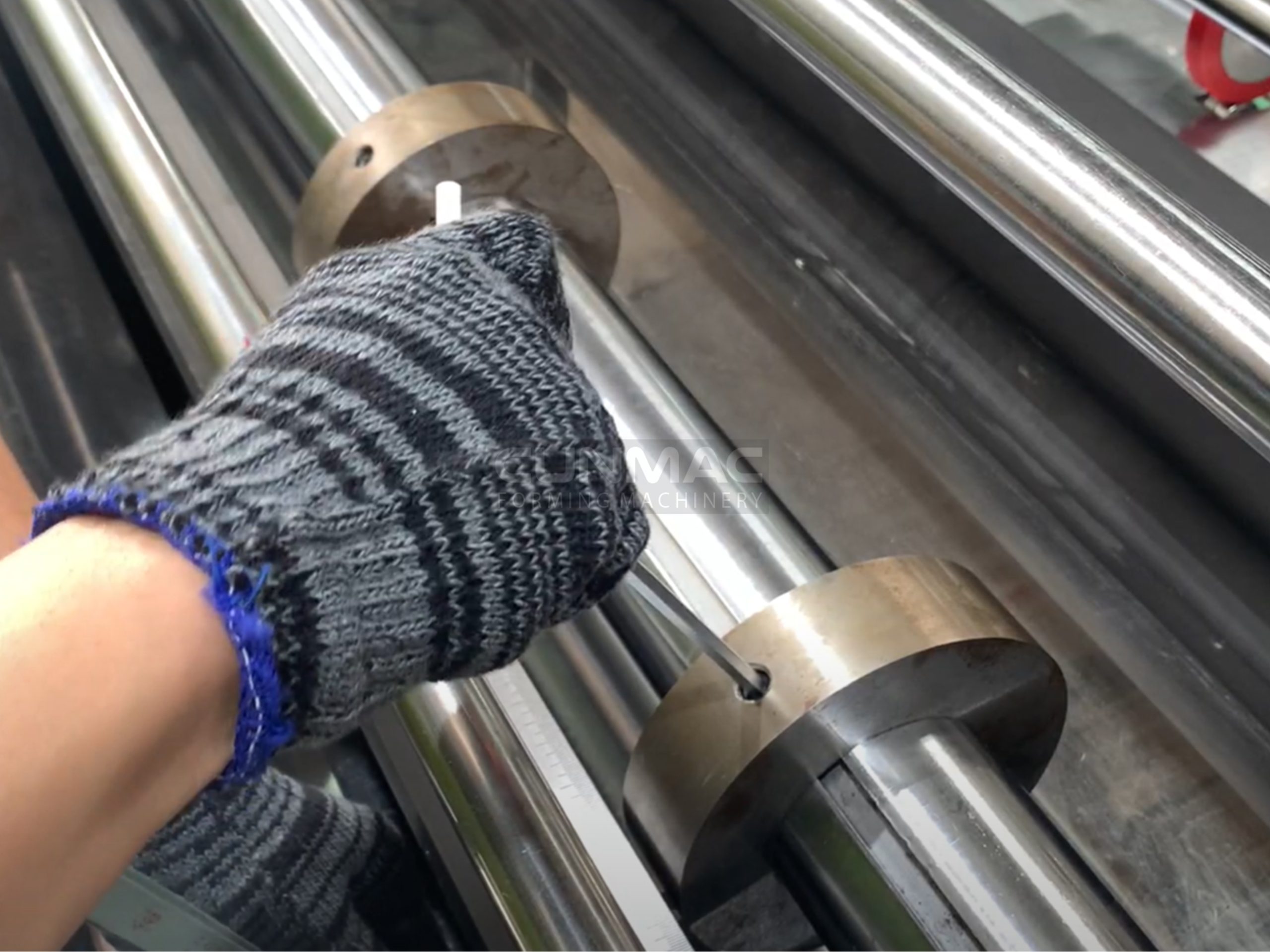
Adjustable stripper blade
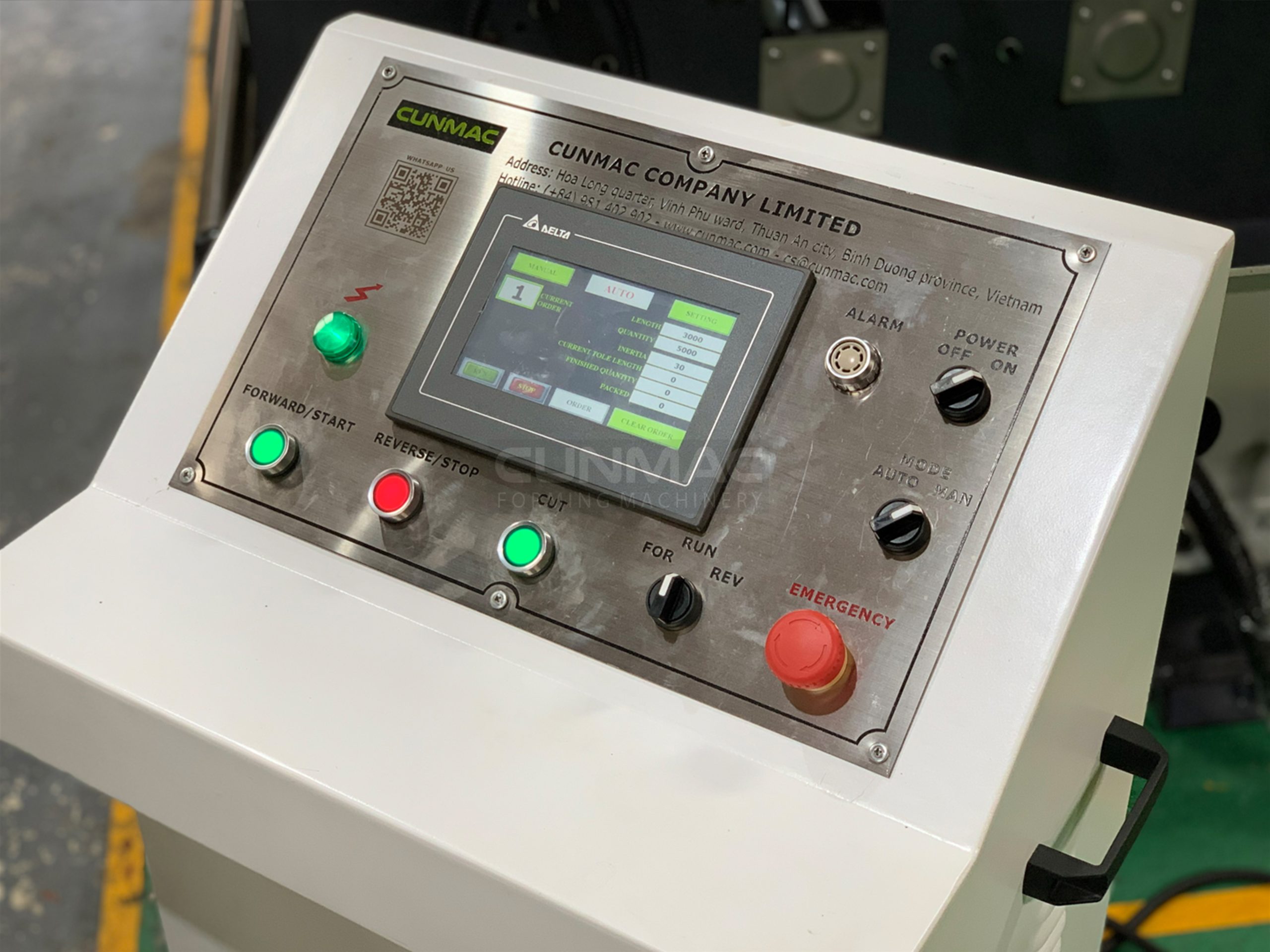
Automatic programmble length settings via touch panel
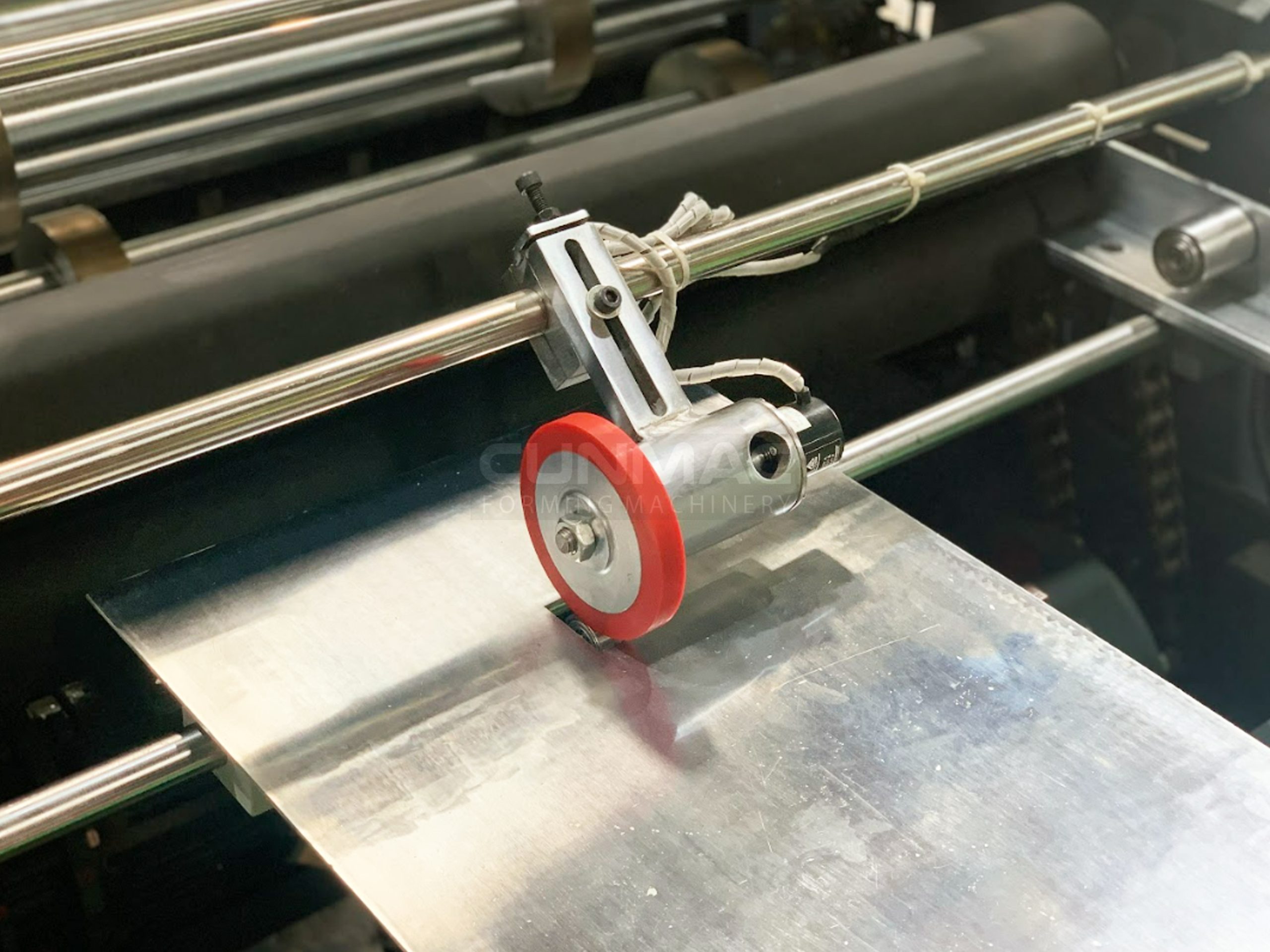
Encoder to count the length of materials
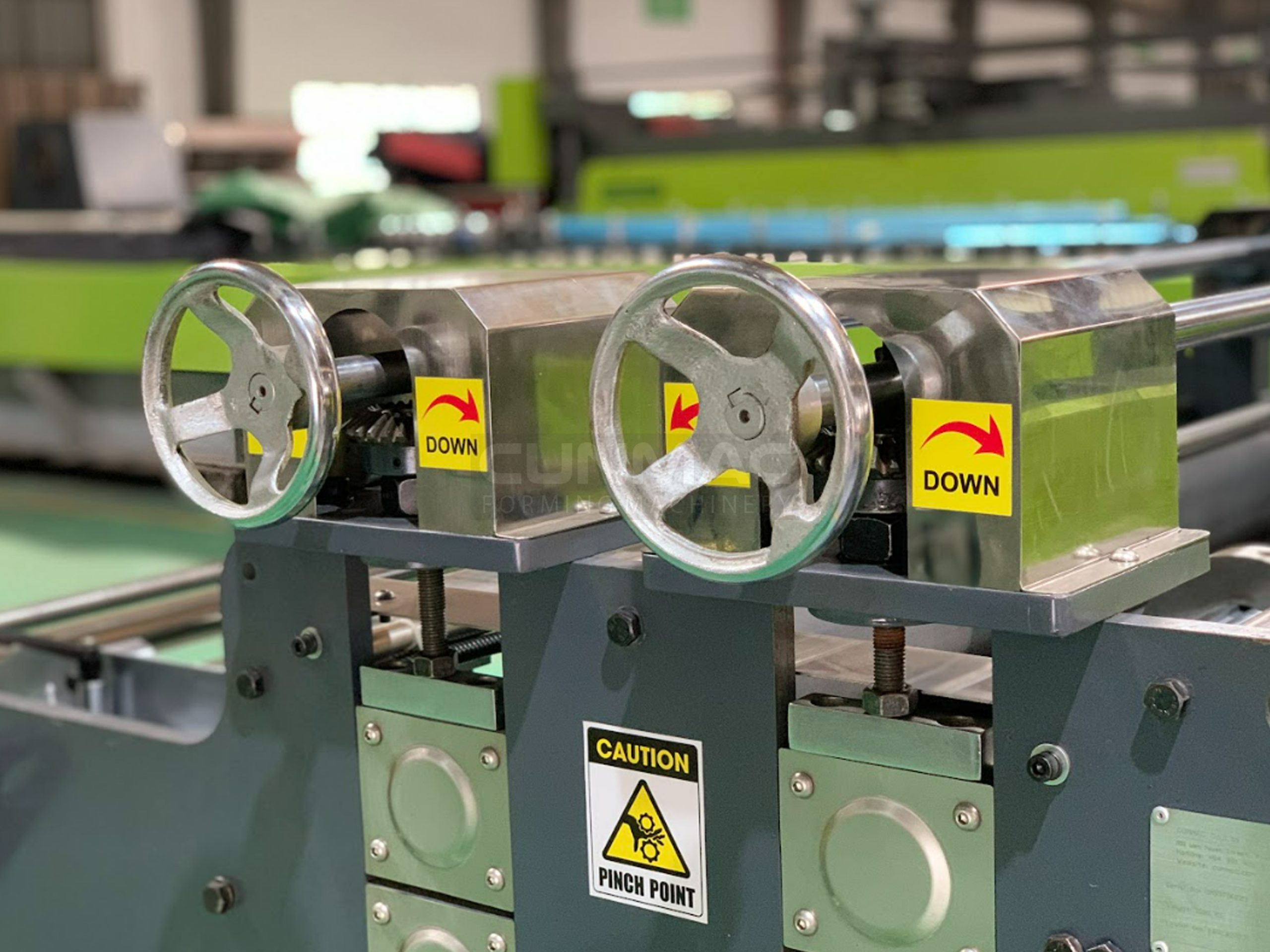
Up and down system for quick adjustment
This machine integrates both slitting and shearing functions, making it highly versatile for operations in the metal slitting and sheet metal shear industries. It effectively handles material thicknesses up to 1.0mm and is widely used in metal processing, laser cutting, and sheet metal applications.
Main advantages:
Rubber roller to guide materials in
Feeding coil can change the width of coil
Adjustable stripper blade
Automatic programmble length settings via touch panel
Encoder to count the length of materials
Up and down system for quick adjustment
Specifications | |
Motor for transmission | 2.2kW (3 phases, 50Hz, 380V)_Inverter 3.7kW |
Motor for shearing/cutting | 2.2kW (3 phases, 50Hz, 380V) |
Slitting speed | 20 – 30m/min |
Dimension: (LxWxH) | 1.8×1.9×1.3m |
Weight of machine | 1.5 tons |
Slitting blade | 3 sets |
Material thickness | 0.2 – 1.0mm (G300 – G550) |
Material width | 400 – 1250mm |
Transmission system | Gear motor with Inverter |
Cutting system | Gear motor |
Changing slitting blade | Manual |
Control system | Automatic with inverter, PLC, HMI |
Input 10 orders, automatic cut to length | |
Save history for orders in 30 days |
Branded equipment | |
PLC (CPU) | SIEMENS (Germany) |
Touch panel (HMI) | DELTA (Taiwan) |
Gear motor | Taiwan |
Encoder, relay | OMRON (Japan) |
Inverter | MITSUBISHI (Japan) |
Cutting & Slitting blades | SKD11 (Japan) |
Designed mainly for slitting, this slit machine is perfect for applications needing a reliable sheet metal slitter and roll slitting machine. It can handle materials up to 1.0mm thick and is commonly used in metal processing, laser cutting, and sheet metal industries.
Main advantages:Â
Safety cover
Rubber roller to guide materials in
Feeding coil: Change the width of coil
Adjustable stripper blade
Specifications | |
Motor power | 2.2kW (3 phases, 50Hz, 380V)_Inverter 3.7kW |
Slitting speed | 20 – 30m/min |
Dimension(LxWxH) | 1.5×1.6×1.3m |
Weight of machine | 0.8 tons |
Slitting blade | 3 sets |
Material thickness | 0.2 – 1.0mm (G300 – G550) |
Material width | 400 – 1250mm |
Transmission system | Gear motor with Inverter |
Changing slitting blade | Manual |
Control system | Auto forward & backward by button and remote control |
Branded equipment | |
Gear motor | Taiwan |
Inverter | MITSUBISHI (Japan) |
Slitting blades | SKD11 (Japan) |
Both the slit machine and slit and shear machine are highly portable, allowing for easy transportation and setup in various locations for maximum convenience.
These machines are a cost-effective solution in the slitting line and cut-to-length line markets, offering excellent value without compromising quality.
Equipped with top-tier components from Japan and Germany, they are quality-controlled and trusted in over 30 countries in the steel slitting and hydraulic metal shear industries.
Backed by a 2-year warranty and 24/7 sales service, these machines ensure long-term reliability in slitting and shear brake roll applications.
Sheet metal factory/Industrial fabrication
The slit and shear machine, when combined with decoilers/recoiler, uncoils the sheets or coils for further processing, preparing the materials for continuous stages.
Automatic Decoiler -> Slitting & Shearing machine -> Automatic Recoiler
Roofing and frame factories
The slit and shear machine, when combined with an uncoiler and recoiler, helps in creating smaller metal sheets or coils. These smaller units are essential for specific applications such as bending, capping, frame, gutter, etc., which increases production efficiency by reducing manual labor and speeding up the workflow.
Capping machine and bending machine used for continuous process after slit and shear materials
We, as an innovative engineering machine manufacturer (OEM), believe in building partnerships and providing comprehensive customer services by customizing design and solutions of roll forming machines for companies operating in the sheet metal, construction and manufacturing industries in over 30 countries worldwide.
Our over 15 years’ experience in manufacturing metal roll forming machines is a result of our high quality awareness to operate in a continuously innovative process. All parts of products fabricated from alloy steel by CNC precision machines.Â
Electrical and hydraulic components derive from reputable brands such as Siemens, Schneider, OMRON, Hitachi, Yuken…
Fill this form now to receive our catalog, exclusive updates, and special discounts directly to your inbox!